CONSTRUIRE LA DÉCARBONATION
Face à l’urgence climatique, le secteur du bâtiment doit relever trois défis cruciaux afin d’atteindre la neutralité carbone d’ici 2050 : décarboner, rénover, recycler. Architectes, maîtres d’ouvrage, bureaux d’études et constructeurs s’adaptent ainsi aux nouvelles exigences de la construction décarbonée. S’appuyant sur la mixité des matériaux et l’économie circulaire, la filière acier-construction s’implique depuis des années dans la réduction de l’impact carbone de la construction métallique : du cœur de la sidérurgie avec la production du matériau à la déconstruction de l’ouvrage.
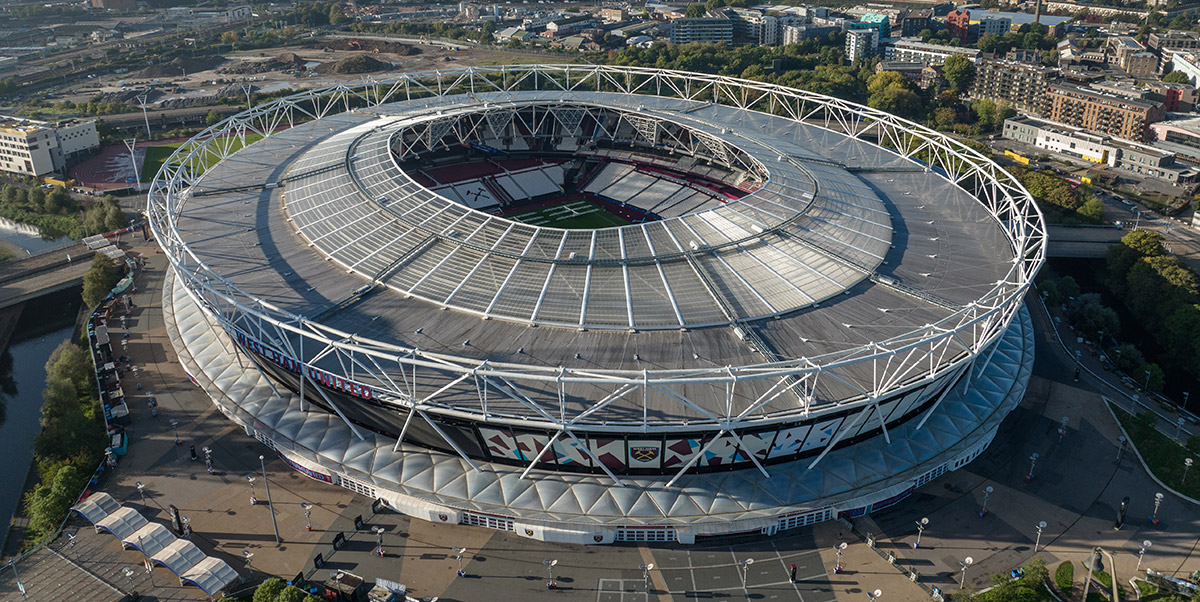
Ériger des bâtiments moins énergivores implique de prendre en compte leur empreinte carbone. La décarbonation d’un édifice -un des objectifs majeurs de la réglementation RE2020 applicable aux constructions neuves- consiste à mettre en place des mesures et techniques vouées à réduire les émissions de gaz à effet de serre (GES), en particulier de CO2. Pour un ouvrage neuf, les matériaux de construction représentent entre 60 et 90 % de leur empreinte carbone. Les acteurs de la construction neuve et de la rénovation du bâti existant –architectes, maîtres d’ouvrage, promoteurs, bureaux d’études, entreprises…- sont engagés à réduire les émissions de carbone de 30 à 40 % à l’horizon 2030 et utiliser des matériaux de construction émettant peu de GES durant leur cycle de vie. Cette réduction porte aussi bien sur les pratiques de conception des projets d’architecture que sur la mise en œuvre des ouvrages sur les chantiers. Or depuis longtemps, la filière acier est fortement engagée dans la diminution de l’impact carbone de la construction métallique.
« LE BON MATÉRIAU AU BON ENDROIT »
LA FILIÈRE ACIER, FER DE LANCE DE LA CONSTRUCTION BAS CARBONE ET DE L’INNOVATION
Pour atteindre ces objectifs contraignants, les diverses filières industrielles sont poussées à innover en permanence et proposer de plus en plus de matériaux dits bas carbone, telle la filière acier-construction située en première ligne dans ce contexte évolutif, soumis à un processus industriel de pointe. L’acier possède de nombreux atouts, comme une empreinte carbone remarquable et une structure métal étant jusqu’à cinq fois moins émissive qu’une ossature béton. Avec un taux de recyclabilité unique de 95% contre 70% pour le béton armé, le métal est disponible en grandes quantités et recyclable à l’infini. À noter que 12 tonnes d’acier sont recyclées dans le monde chaque seconde, tandis que le béton armé est en général transformé en ballast après la démolition d’un édifice. L’acier répond aux exigences énergétiques des bâtiments, où des façades sur-isolées procurent un haut degré de confort thermique aux espaces habités, en réduisant les consommations. Sa durabilité autorise de densifier l’habitat, en utilisant moins d’emprises foncières et en érigeant des immeubles hauts, au-delà de huit niveaux. L’acier contribue donc à réaliser des projets à faible empreinte carbone, vision à mettre en perspective avec les performances d’autres matériaux tels que le bois et les biosourcés pour arriver au meilleur compromis en conception. Mieux encore, avec les innovations de l’industrie sidérurgique comme la réduction directe du fer, l’hydrogène vert, la séquestration et le recyclage du C0²et, bien sûr, le recyclage des ferrailles, les aciers décarbonés qui offrent les mêmes qualités et propriétés que l’acier traditionnel s’imposent d’ores et déjà dans la construction. Dès aujourd’hui, des sidérurgistes proposent sur le marché français des produits et composants acier de structure et d’enveloppe dont l’empreinte carbone par unité fonctionnelle (1 m2 de bardage ou toiture ou 1 m de poutre) est fortement réduite. Elle est effectivement divisée par au moins trois par rapport aux aciers classiques. Ces solutions font l’objet de FDES (fiches de déclaration environnementale et sanitaire) déjà publiées ou à venir pour répondre aux exigences de la RE 2020 et plus largement d’EPD (Environmental Product Declarations) européennes publiées. Production-construction du bâtiment, vie en œuvre et fin de vie : trois voies pour améliorer efficacement le bilan carbone des bâtiments avec les aciers d’aujourd’hui et de demain. Les solutions acier bas carbone sont donc dorénavant une réalité.
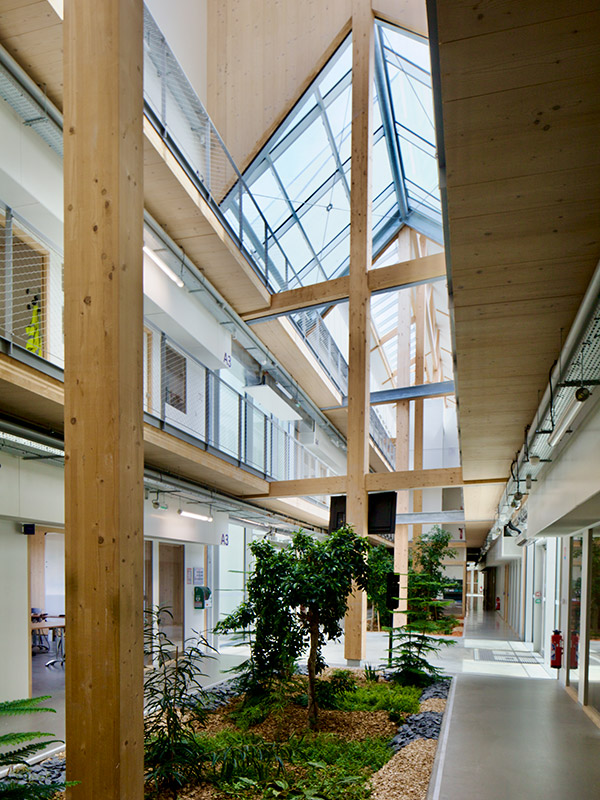
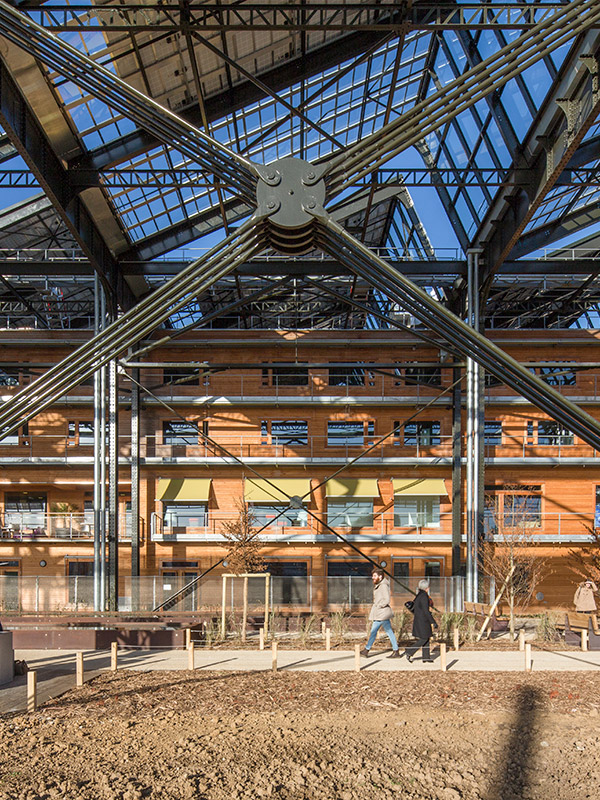
CONSTRUIRE AUTREMENT, PRIVILÉGIER LA MIXITÉ DE MATÉRIAUX ET D’USAGE
Si l’acte de construire a longtemps consisté à bâtir un ouvrage à l’aide d’un matériau, tel que le béton, le bois, l’acier…, avec des équipes dédiées à la structure, les façades.., les architectes revendiquent aujourd’hui un mode opératoire différent, collaboratif et pluri-disciplinaire, où interviennent divers corps de métiers, tels qu’ingénieurs, urbanistes, acousticiens, paysagistes… Répondre à un projet complexe requiert une démarche conceptuelle sobre et à bas carbone, intégrant une étude approfondie de l’impact carbone sur le cycle de vie complet de chaque combinaison de matériaux, que ce soit en neuf ou en réhabilitation. Les capacités propres de chaque matériau sont pleinement exploitées si « le bon matériau est mis au bon endroit » dans l’édifice afin de garantir sa tenue dans le temps, au sein d’une construction frugale et économique. Les systèmes constructifs en ossature acier, formés de profils préfabriqués facilement mis en œuvre en filière sèche, allègent le bâtiment et le rendent plus flexible. L’organisation des chantiers évolue elle aussi vers une rationalisation et sécurisation des tâches, avec moins de déchets. L’agence d’architecture Hobo a réhabilité en 2019, sur la ZAC Niel à Bordeaux (33), un immeuble (bureaux-logements) Bord’ha, mixant fonctions et matériaux. Quatre niveaux ont été greffés, en toiture et en charpente acier, au-dessus de l’ancien économat SNCF en béton, les éléments légers en acier s’adaptant à tout type de morphologie créée. Autres programme et expression avec le pôle Viotte réalisé en 2023 à Besançon (25), sur une ancienne friche ferroviaire, par l’architecte Brigitte Métra. Cette cité administrative, dédiée à des services d’Etat de la région, compte notamment trois halles innervées par une rue-jardin. Bâties en ossature bois et acier, et planchers bois CLT, ces entités se lovent sous des verrières éclairant naturellement les espaces de travail, les façades virées se dotant de châssis aluminium.
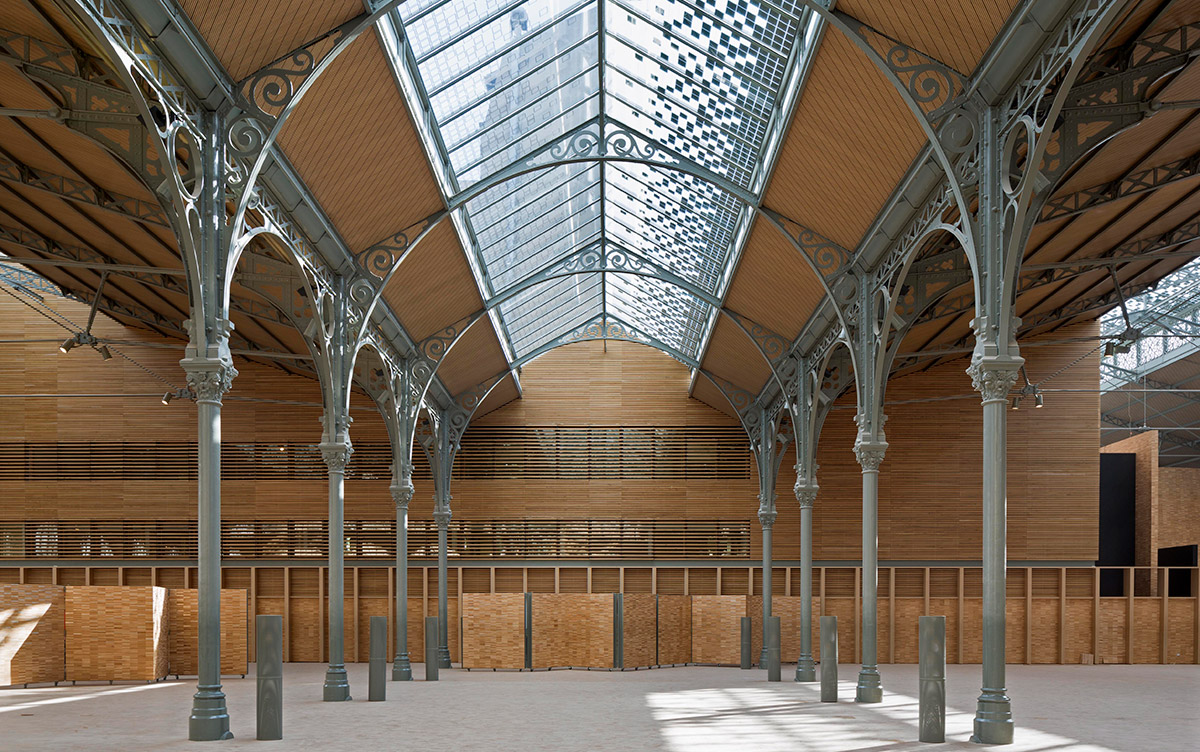
FAVORISER LA RÉNOVATION ET/OU LA RECONVERSION D’UN ÉDIFICE
En termes de développement durable, la réhabilitation, rénovation et/ou reconversion du bâti existant sont conseillées pour éviter de démolir et reconstruire un édifice en place, plus polluant et souvent plus coûteux que sa restructuration, alors que le secteur de la construction représente 23% des émissions de GES françaises. De multiples opérations de ce type ont vu le jour ces dernières années, les architectes œuvrant dans un contexte économique tendu, dominé par une recherche de sobriété et de frugalité incontournable. Il s’agit de rationnaliser la pose des matériaux et leur combinaison entre eux, tout en conservant le plus possible les structures existantes d’un édifice et son architecture unique. Et rien n’empêche d’ajouter des éléments contemporains aux bâtiments en place, comme pour la halle Pajol à Paris 18è (1926) restructurée en 2009 en une auberge de jeunesse, par l’architecte Françoise-Hélène Jourda. Sous la charpente métal des dix sheds remaniés, se glisse un parallélépipède en composants de bois, les planchers étant en béton et le toit couvert d’une centrale photovoltaïque de 3 500 m² pourvoyeuse d’électricité. De même, pour le Carreau du Temple à Paris 3è (1863) transformé en équipement culturel en 2014 par le Studio Milou Architecture. Si sa charpente métallique est savamment restaurée, ses façades en métal et verre sont sur-isolées, tandis que les pans sud des trois verrières, revêtus de cellules photovoltaïques, baignent le volume de lumière naturelle.
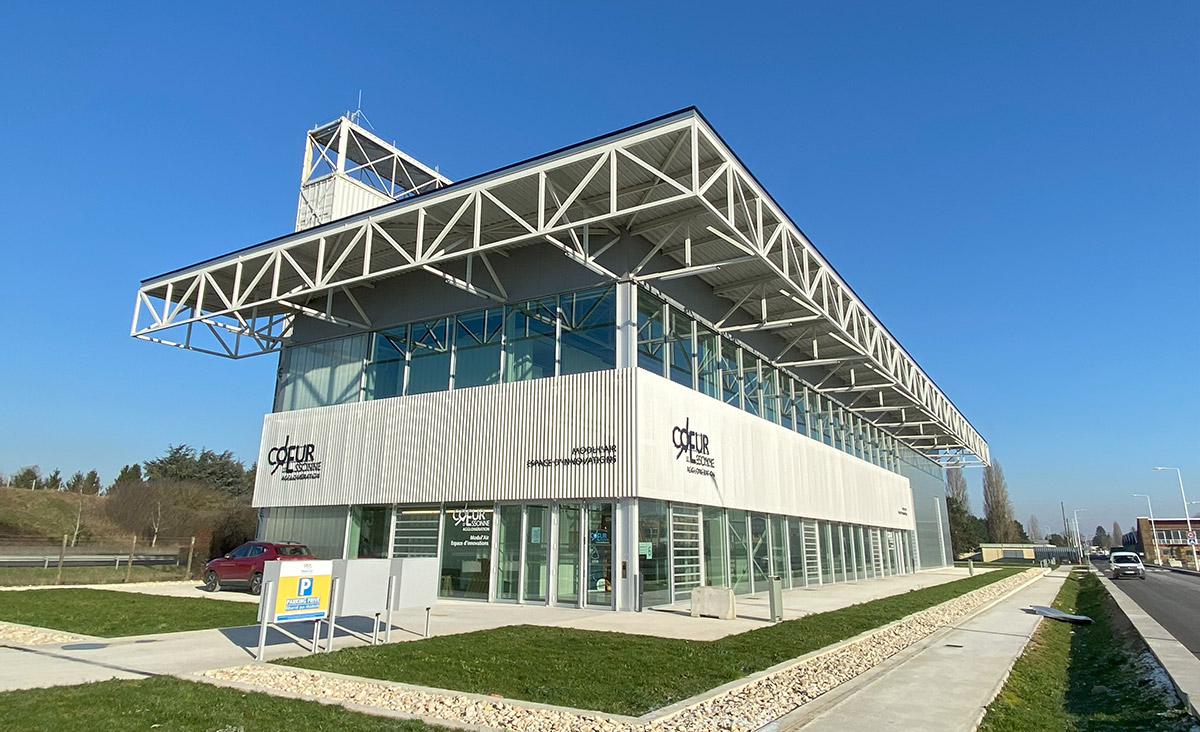
LE HORS-SITE, LEVIER MAJEUR DU BAS CARBONE
Le mode de construction hors-site en plein essor est très performant sur les plans économique, environnemental et de rapidité de chantier. L’acier est omniprésent, puisque ce matériau léger et maniable est aisément transporté depuis les ateliers de fabrication jusqu’au site d’assemblage, sans devoir mobiliser une flotte de véhicules. La circulation des camions sur chantier, qui baisse d’environ 39% dans le cas de la construction hors-site, génère une diminution notoire des émissions de carbone. L’industrialisation de la construction acier, qui passe par des composants standards, réduit le nombre de pièces à poser et le temps de pose sur le chantier. S’il s’agit le plus souvent de structures préfabriquées en usine, posées in situ, l’exemple ultime est celui de containers acier réutilisés pour bâtir des ouvrages. Le concept de modularité est propice à la préfabrication de modules, car les éléments -voiles, dalles et enveloppes (acier ou bois)- sont fabriqués en usine, puis livrés et assemblés sur site. Ce principe, qui s’appuie sur la capacité d’un édifice à évoluer par remplacement, ajout ou soustraction d’éléments structurels ou composants de façade, simplifie le démontage futur du bâtiment, en vue d’un réemploi des matériaux. Les modèles combinant préfabrication hors-site et diversité des matériaux gagneront à être explorés. Hors-site oblige, le bâtiment Modul’Air réalisé en 2021 à Brétigny-sur-Orge (91) par les agences LFA et Calq, abrite des bureaux et locaux dédiés à des entreprises liées à la recherche et l’innovation. Il est bâti, à l’aide de 18 containers maritimes préfabriqués -peints et pré-équipés en usine selon leur fonction- qui se glissent sous un parapluie géant constitué d’une ossature à profils d’acier standard.
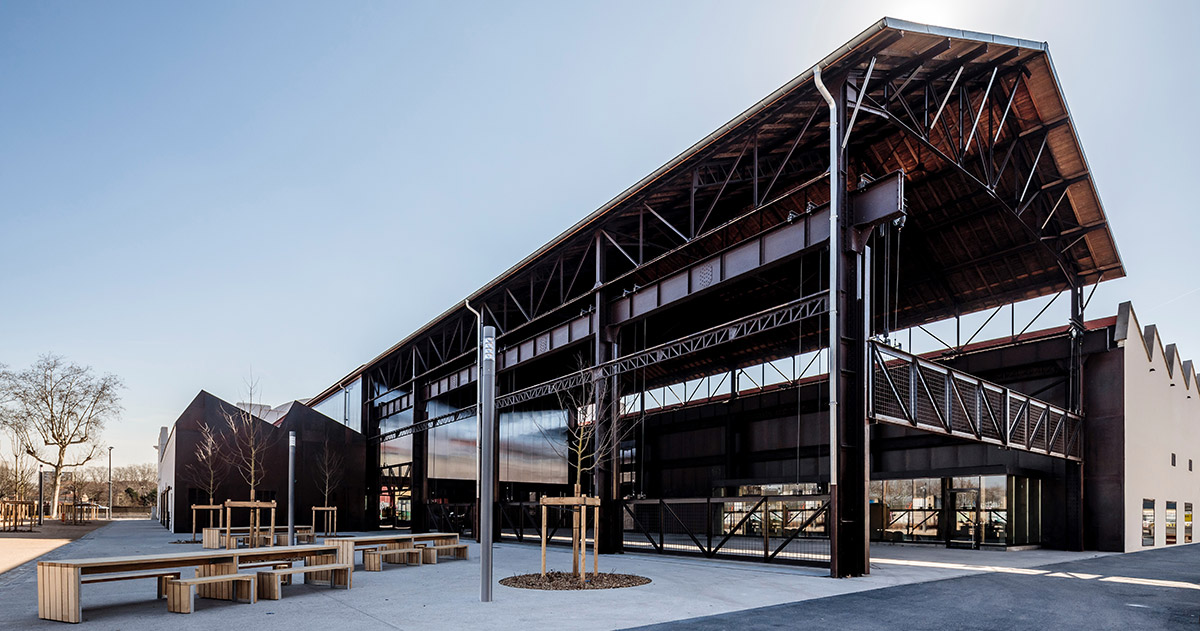
DÉVELOPPER LE RÉEMPLOI ET L’ÉCONOMIE CIRCULAIRE
Conserver les bâtiments existants en limitant les démolitions reste l’un des principaux leviers de la neutralité carbone à atteindre, démolir pour reconstruire émettant plus de CO2 que bâtir un ouvrage neuf. Les architectes et acteurs soucieux d’écologie développent le réemploi, dans une perspective d’économie circulaire qui consiste à réutiliser les matériaux de construction provenant de bâtiments ou de sites industriels, en garantissant leurs performances mécaniques et en réduisant les déchets. Cette approche nécessite une collaboration renforcée entre les différents acteurs de la filière et une planification rigoureuse dans l’acte de construire entre conception, construction et identification d’un gisement de réemploi. Les projets de réemploi sont en plein essor et adaptés aux produits acier durable qui, voués à être déconstruits en fin de vie d’un édifice, peuvent être réemployés tels quels ou bien remis en état. L’émergence de plateformes de réemploi de matériaux issus de chantiers de démolition permet de mener à bien des projets pionniers. Le stade olympique de Londres, au Royaume-Uni, bâti en 2011 à Stratford par l’agence Populous et Sir Peter Cook architecte, a servi de site d’athlétisme pour les Jeux olympiques d’été de 2012, avant d’être rénové en 2016 pour être plus polyvalent. Son toit en charpente acier, démontable et transformable, est muni de câbles tendus dotés d’un anneau central servant de passerelle, l’anneau externe comptant un treillis en tubes, issu de la récupération de pièces en métal d’un ancien gazoduc. De même pour le One World Trade Center, érigé à New-York en 2014 par les architectes Skidmore, Owings & Merrill, en lieu et place des tours jumelles disparues en 2001. Cette tour élancée -de 542 m de haut et 104 étages- comprend une solide structure en poutrelles et plaques d’acier, dont environ 90% proviennent d’aciers recyclés dans la construction. Pour les halles industrielles Girard Sudron (1843) à Ivry-sur-Seine (94), elles ont été restaurées en 2019 par l’architecte Loïc Julienne de l’agence Construire et reconverties en une manufacture de mobilier, où les ateliers de conception et fabrication des designers Maximum produisent du mobilier en série, à partir de déchets issus d’industries françaises. La réhabilitation a été exécutée, en majorité, à partir d’éléments réemployés, l’acier constituant les charpentes et menuiseries.
Les galvanisateurs passent à l’action
Qu’il s’agisse d’énergies avec notamment la récupération de la chaleur des fours ou l’utilisation du biogaz, de la protection des ressources (bassins de rétention , recyclage et revalorisation des matières) ou encore de transport, les galvanisateurs multiplient les actions en faveur de la préservation de l’environnement et s’impliquent plus que jamais sur la voie de l’économie circulaire.
Spécialisé dans le traitement anticorrosion de l’acier, Prestia est ainsi actionnaire d’une société productrice de biogaz à partir de déchets agricoles réalisant ainsi des économies de l’ordre de 275 tonnes de CO2. Utilisant du zinc sans plomb et du zinc SHG produit avec des énergies bas carbone, l’entreprise multiplie les projets pour la production d’énergies décarbonées, la réduction des consommations d’énergies, la réduction de l’utilisation des ressources primaires. Certifiées ISO 9001, 14001 et 45001, Prestia adhèrent aux objectifs de développement durable des Nations Unies (COP 21) et est en cours de certification SDG Pioneer. De son côté, Le Groupe Louis a fait construire sur le site de Galvamétal, un immense hangar de stockage des pièces galvanisées dont la toiture est intégralement couverte de panneaux solaires (750 kW en autoconsommation totale). Récupération des gaz chauds des fours gaz pour les séchoirs et/ou bains, recyclage et revalorisation des matières, emploi du zinc recyclé ou bas carbone, utilisation des eaux de bassins de rétention extérieurs sur les bains de deux usines, formation des conducteurs à l’écoconduite, acquisition d’une flotte de véhicules électriques… : autant d’actions militant en faveur de la dévarbonation et de la protection de l’environnement. Les producteurs de zinc, quant à eux, élaborent du zinc bas carbone, en électrifiant les sites de production, en utilisant des énergies renouvelables (éolienne, hydraulique), en récupérant de la chaleur excédentaire générée pendant la production. Ils produisent également du zinc provenant du recyclage et de la récupération, zinc bas carbone tout en utilisant le transport ferroviaire et fluvial, fret neutre en carbone…
CENTRE D’HÉBERGEMENT D’URGENCE L’HESTIA, PÉRIGUEUX (24), AGENCE MOONARCHITECTURES
HORS-SITE ET CONTAINERS MAGNIFIÉS
Dans le quartier de Toulon de Périgueux (24), le centre d’hébergement d’urgence L’Hestia -du nom de la déesse grecque du foyer- réalisé en 2020 par l’agence Moonarchitectures, remplace les chalets et mobile-homes du site logeant auparavant les sans-abris. L’ensemble, de 46 logements et 1 300 m², bâti pour une centaine de résidents, compte un premier édifice R+1 situé près de l’entrée et dédié aux familles, et un second R+2 placé à l’arrière et destiné aux individus seuls en autonomie ou intégrés dans un parcours de réinsertion. « Le lien entre les deux bâtiments est assuré par un vide central, traité en espace vert et agrémenté de bancs et d’un terrain de pétanque.», précise l’architecte Guillaume Hannoun. Outre les chambres, ces deux unités abritent deux cuisines et deux salles de restauration ainsi que des bureaux et des salles de réunion voués aux travailleurs sociaux. À chaque étage, les espaces de transition -qui ouvrent vers l’extérieur et à l’abri de la pluie- sont adaptés aux résidents ayant souvent vécu à la rue. Côté structure, le défi de ce chantier a été de construire les deux entités en seulement neuf mois, dont trois en atelier, grâce à la mise en œuvre d’un système constructif hors-site performant. Ce dernier consiste à réutiliser 51 anciens containers maritimes en acier durables, pré-équipés en atelier (menuiseries, cloisons,..) et « isolés extérieurement pour assurer la continuité de l’enveloppe thermique habillée. », ce qui leur octroie une empreinte carbone faible et un bilan environnemental de qualité. Les façades en long pan ou en pignon, bardées de bois ou d’acier, enrichissent l’expression minimaliste de cette opération sociale.
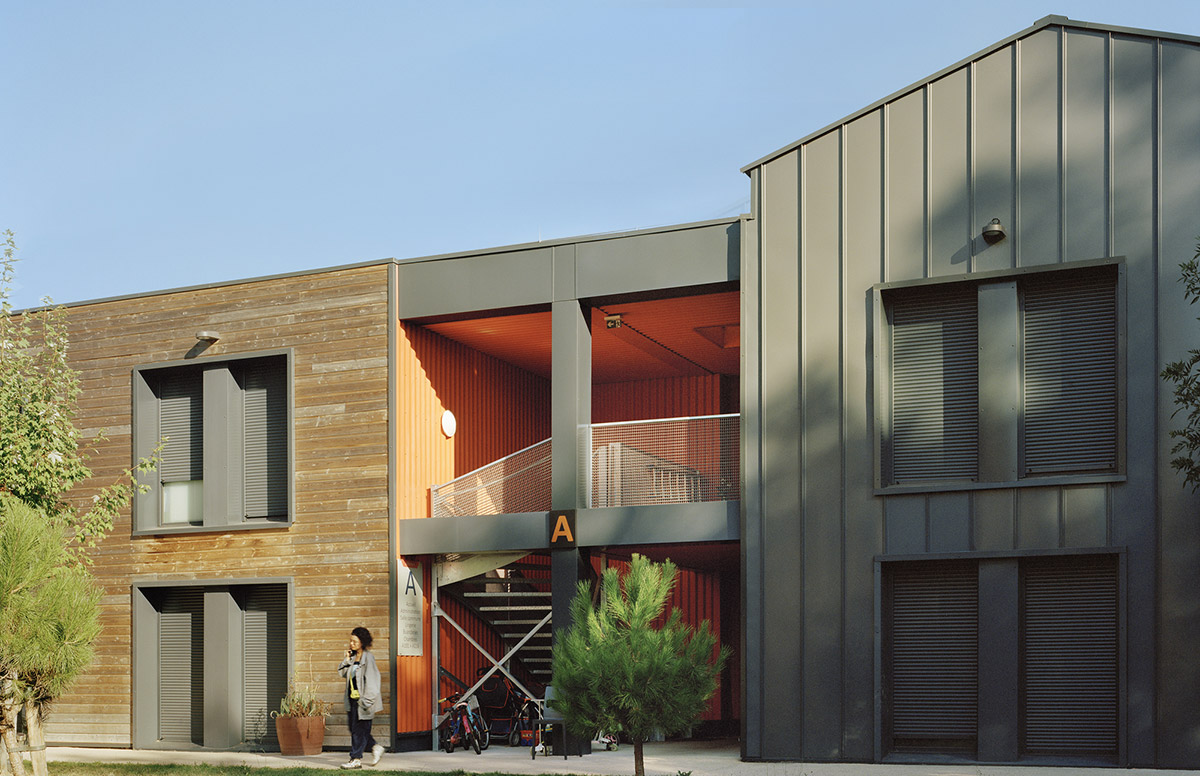
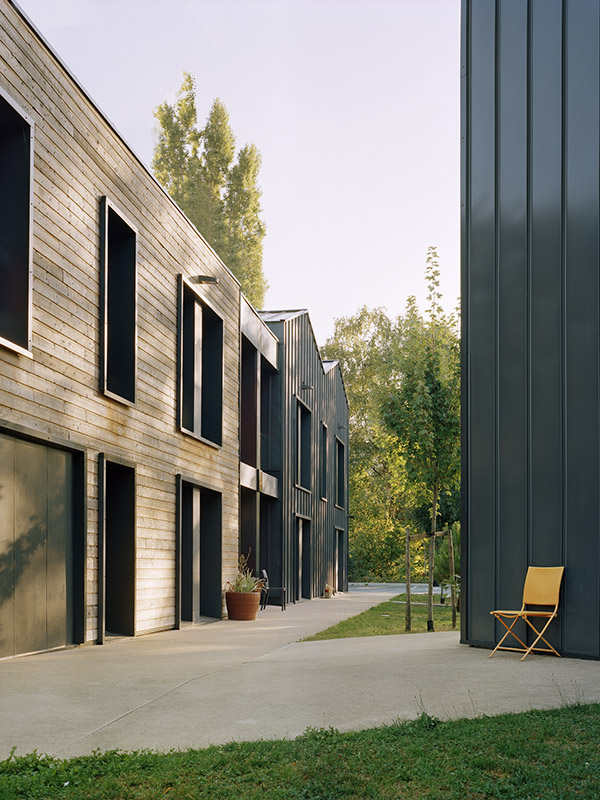
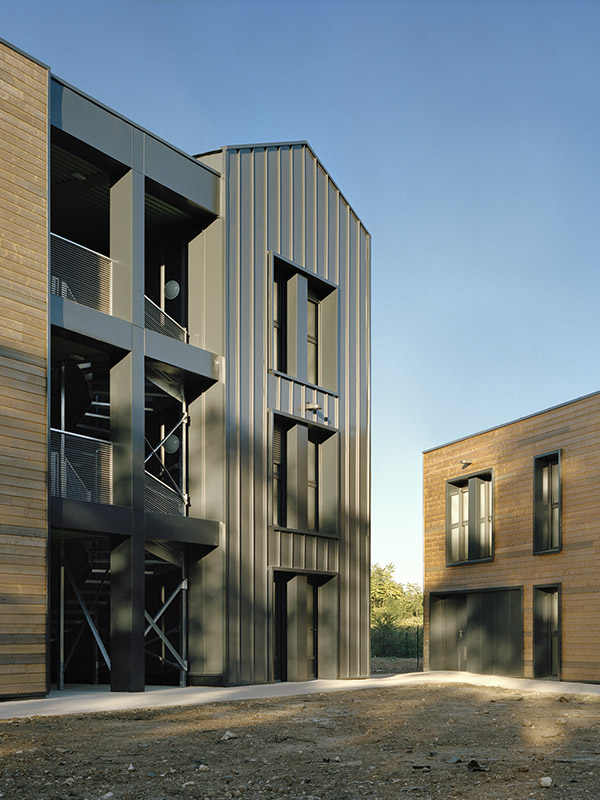
ATELIER DE MAROQUINERIE LOUIS VUITTON, BEAULIEU-SUR-LAYON (49), DE-SO ARCHITECTES
UN MECCANO ÉPURÉ EN ACIER ET BOIS
Construit à Beaulieu-sur-Layon (49), dans la vallée de Layon, le 16è atelier de maroquinerie Louis Vuitton a été conçu en 2019 par DE-SO architectes. Le parallélépipède aérien et épuré mesure100 m de long, 30 m de large et 6 m de haut. « La conception architecturale et technique privilégie l’économie de matière, dans une efficience structurelle et une organisation simplifiée des réseaux techniques, précise l’architecte François Defrain. Le concept « agile » de l’atelier répond à trois critères principaux : la rapidité d’exécution, la souplesse d’utilisation et la capacité d’évolution.» Le plan libre et ouvert de 6 000 m² se déploie sous une charpente mixte acier-bois, ponctuée de seulement six poteaux métalliques, l’espace de production comportant des « boîtes-dans-la-boîte » qui logent des bureaux aptes à être reconfigurés. La charpente optimisée assemble in situ, à l’aide de goussets, des poutres transversales hybrides qui, franchissant 30 m sans point porteur, sont constituées de deux membrures hautes en bois lamellé-collé (BLC) et d’une charpente treillis en profils standard. « Ces poutres triangulaires rythment l’espace intérieur de l’atelier, telle une succession de voûtains.» Espacées de 5 m, ces poutres, intégrant les gaines de réseaux, sont disposées en « arêtes de poisson », attachées entre la poutre longitudinale de centre de la halle et les poteaux de façade dédoublés à 2,50 m. Si la couverture est pourvue de panneaux en CLT fixés sur les membrures en BLC de la charpente, les façades -dotées de vitrages ou de MOB préfabriqués, en fonction de leur emplacement- sont modulées selon la même trame de 2,50 m de large et 6 m de haut.
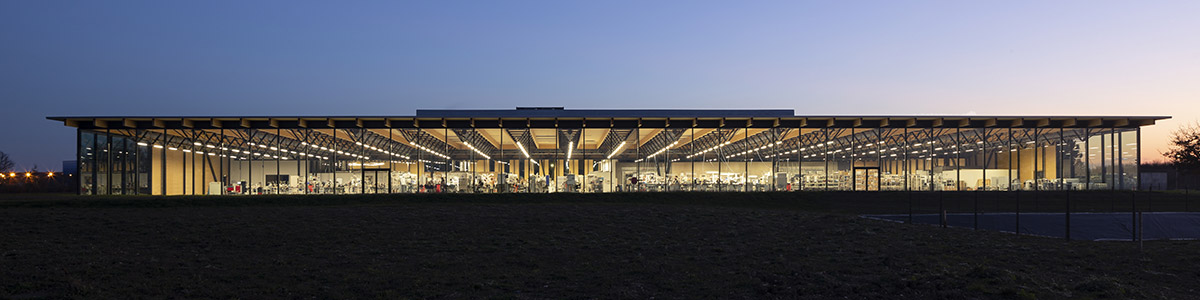
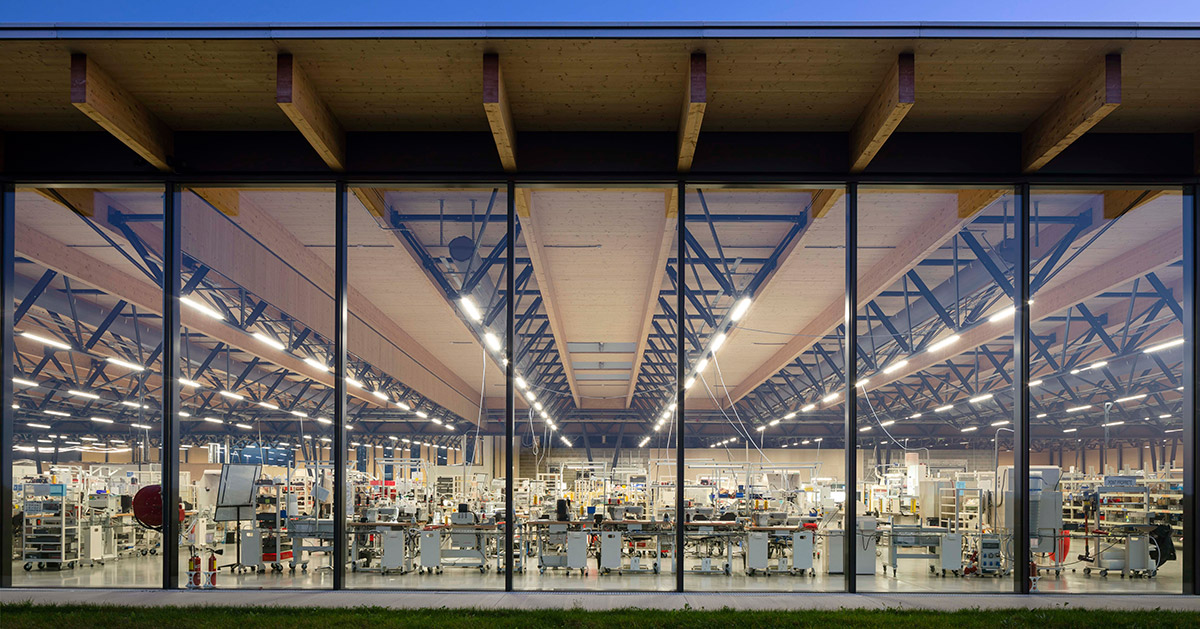
PASSERELLE VELODUKT, ESCH-SUR-ALZETTE/BELVAL, LUXEMBOURG, JIM CLEMES ASSOCIATES
MATÉRIAUX À FAIBLE EMPREINTE CARBONE ET INSERTION PAYSAGÈRE
Cette passerelle VëloDukt pour cyclistes et piétons relie Esch-sur-Alzette au quartier d’Esch-Belval, au Luxembourg. Inaugurée fin 2022, cette piste cyclable surélevée –qui s’élève à 7,50 m de haut et s’étire sur 1,2 km de long, en passant par l’usine Belval d’ArcelorMittal et la gare centrale- a été conçu par l’atelier Jim Clemes Associates. « Elle permet une circulation fluide et sécurisée, au travers d’un paysage contrasté, témoin d’un riche passé sidérurgique, indique l’architecte Jim Clemes. Si sa structure reflète le choix des matériaux, des teintes utilisées et de l’ordonnancement de ses composants, l’ouvrage réinterprète, de manière contemporaine, le langage architectural et émotionnel de ce lieu si particulier.» La conception durable de cette passerelle a requis l’utilisation de matériaux de construction à faible empreinte carbone. Si les piles de support du tablier sont en béton, ArcelorMittal a fourni, pour la charpente métallique, des profilés de la gamme XCarb®, produits à partir de 100% de ferraille recyclée –dont certains sont en acier autopatinable Arcorox®-, avec des sources d’énergie renouvelable (éolienne et solaire). Cet acier spécial, qui détient une empreinte carbone réduite de 0,3 tonnes de CO² par tonne de produit, est certifié par une déclaration environnementale de produit (EPD). Le plancher de l’ouvrage compte des profils acier standard (IPE 200 et IPE 600), et sa sous face, 340 tonnes de poutres longitudinales HL 100 épissées en T et 200 tonnes de profils courbes. « Les teintes de recouvrement de la piste, les laquages chatoyants de certaines structures et l’acier autopatinable participent à l’intégration du projet dans son contexte.»
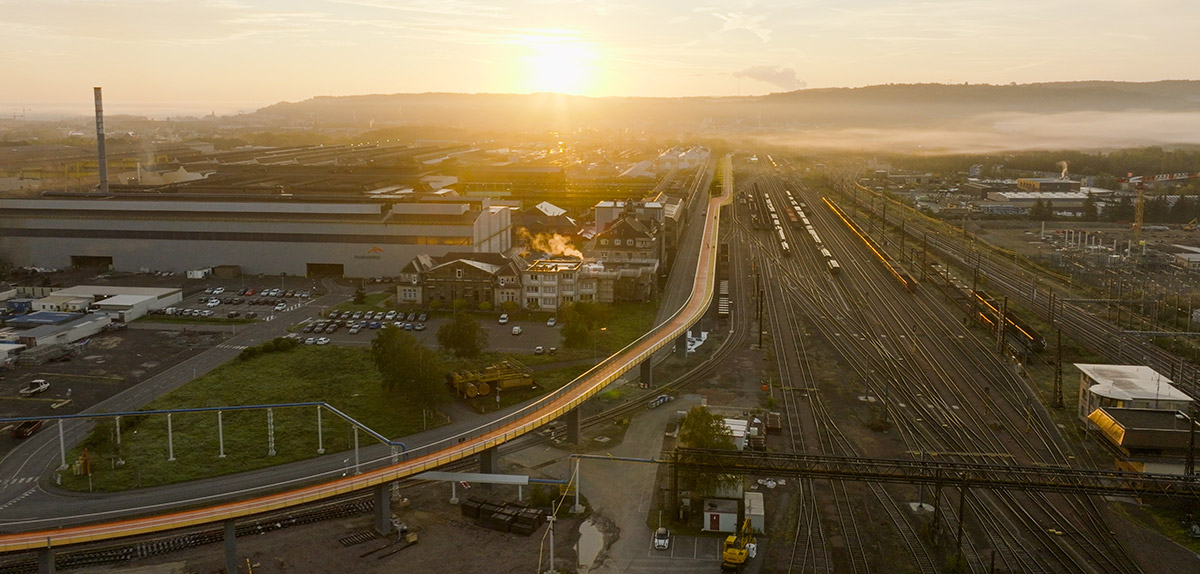